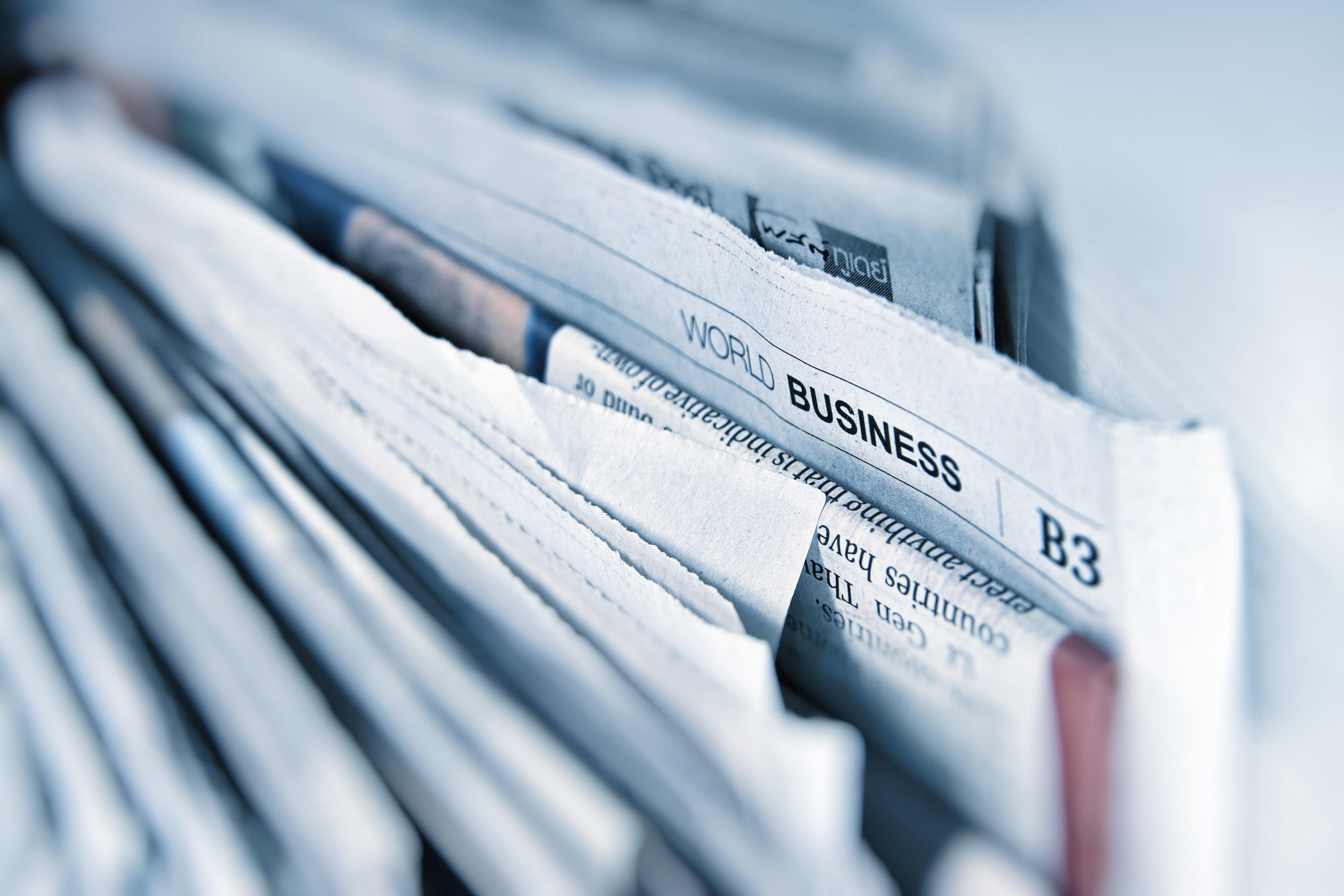
Who Will Be the “Innovators” and “Dinosaurs” of Post-Pandemic Innovation?
Recently, Ron Fritz, CEO of Tech Soft 3D, hosted a roundtable discussion with four other technology executives to discuss what type of innovation is going to gain traction in the post-COVID world.
Mixed reality is set to give the term “connected worker” a whole new meaning. Where are there other opportunities to innovate? Is 3D printing ready for its breakthrough moment? Will “lights out” manufacturing ever be a thing? And can small, innovative point solutions successfully take on the big, monolithic platforms?
Offering their thoughts on these and other matters are:
- Patricia Hume, CEO of Canvas GFX, drawing, imaging, and publishing software
- Michael Bogomolny, Co-founder and CTO of Paramatters, generative design software
- Magnus Gäfvert, CEO of Modelon, systems modeling and simulation software
- Tyler Barnes, Vice President of Partner Engagement at Tech Soft 3D, 3D development tools for engineering software
A lightly edited and condensed version of the conversation follows.
Q: Where do you think we’ll see the most innovation post pandemic? The world’s been changed by the events of the past year, and we’ve had our eyes opened to new ways of doing things. Where are there opportunities to do things differently in this new world?
Patricia Hume: I’ve heard customers start to talk about their “connected worker” strategy, and I initially thought they meant collaboration, which is kind of old news — but that’s not what they meant at all by “connected worker.” They were talking about having experts strap on a headset and use mixed reality to help with something like fixing an oil rig out in the field. I see that increased usage of augmented reality and virtual reality coming, and I see it coming faster than anticipated. Partially, that’s because before the pandemic, people might have said “How important is that capability, really?” And the answer, once it became really difficult for people to physically go anywhere during the lockdown was, “I guess this is more important than we thought.”
Of course, one of the bottlenecks to address is you’ve got this cool device like a Microsoft HoloLens. But where are you getting the data? Which to me is the documentation, the images, the animation, and the other stuff you need in order to ensure that the employee has what they need to do their job, whether it’s fixing an oil rig or performing some other task.
Tyler Barnes: I couldn’t agree more. It’s a huge opportunity — the maintenance, repair, and operations space has been rife with inefficiency, and no one’s really cracked the code on it. That’s exciting to see the developments taking place there.
Magnus Gäfvert: We’re coming at maintenance from a slightly different angle of system simulation, which is more about describing the behavior of some kind of complex device or system by means of exploiting the actual physics embedded in the thing. The models can reproduce or predict performance and behavior, which makes us adjacent to some of the buzz around digital twins and predictive maintenance. We’re really thrilled about all the opportunity that we see in this space and think more and more big players are seeing the economic value of moving maintenance processes into the digital space.
Michael Bogomolny: In a way, we’re related to keeping things up and running as well, because we’re focused on generative design and additive manufacturing. If you have a broken component or part out in the field, how quickly can you come up with a replacement part? I think a lot of industries — like oil & gas, or the military — are a natural fit for having the ability to generate valid geometry which can then be additively manufactured to quickly generate a replacement component.
Actually, after the supply chain disruptions that the pandemic caused over the past year, I think you’ll see inroads into a lot more industries, like automotive. Nobody wants their production line shut down because they’re missing one component that someone else is manufacturing for them.
Q: We touched on some aspects of Industry 4.0 above. People sometimes talk about “lights out” manufacturing: being able to have factories run with fewer or no people. It seems like the motivation to do that is even higher now, when people worry about whether there is going to be another pandemic and how they might be able to still safely maintain operations. What are folks seeing around Industry 4.0 and getting to the point that factories can actually run without people?
Patricia Hume: Before we can reach that point, there is a big problem we need to address, which is that the industry is too siloed. There are so many different technologies, and they all live in their own little world. There’s IoT and PLM and digital twin and supply chain and mixed reality and so on and so on.
It’s going to take a while before we truly get to factories that can run people-less, because the market is highly fragmented. There are so many players competing to solve a problem, rather than solving the problem of how to get to Industry 4.0. As technologists, we’re not working together well enough. We’re overlapping, but not integrating.
Michael Bogomolny: I more than agree with you. As a startup, we cannot solve all the problems, because we don’t have the resources — so we solve a particular pain. That’s why the mania for mergers & acquisitions is happening with all the big companies.
Magnus Gäfvert: This is something we have observed from our position for a long time. If you look at the big players, they are building humongous platforms that include all functionality. It must be somewhat scary for a potential customer to say, “Well, we’re going to put all our eggs in one basket, and use that platform for everything we do.” You can’t rely on any provider to offer the best individual solutions for all the different pieces.
The way forward, I think, is to have point solutions that can integrate with other systems. This means putting a lot of effort into building software on open standards with open APIs, and making sure the solution is split up into modules so that it’s not an “all or nothing” package. This vision does not seem to be shared by everyone — obviously, there are some big, monolithic platforms out there — but we believe in it very strongly, and we believe that the importance of open standards and open APIs will continue to increase.
Patricia Hume: I just think it makes sense, because if we’re here to serve our customers, that’s what our customers need. They want integration and compatibility. Opening the systems makes everybody a winner.
Michael Bogomolny: Part of getting to industry 4.0 is also about shaking up established workflows that are in place. For example, automotive companies have certain workflows that have been in place for decades, and certain tools associated with those workflows. Getting new tools in front of them — just having them take a look and evaluate them, rather than sticking with the same thing they’ve been doing for years — is key to getting the ball rolling.
Q: It seems like now would be a really great environment for the growth of additive manufacturing and to get people to actually try it and realize what it can do. But the stock prices of the big 3D printer companies haven’t really reflected that opportunity. How do you explain that? Why do you think on the one hand, the conditions seem so ripe for 3D printing to gain momentum, but on the other hand, the printer companies aren’t making a lot of money?
Michael Bogomolny: It’s an interesting question. Sometimes the market behavior, the investors’ behavior, and the actual companies’ behavior are not aligned. This is exactly what’s happening here. In the beginning of the COVID-19 outbreak, it became very clear that the supply chain was more fragile than people previously thought. Many companies quickly understood that they needed at least some fraction of manufacturing to be local — not all of it, but at least part of it. And if you want local manufacturing and low investment costs, this is where additive manufacturing really shines.
Q: Any final thoughts around innovation and what shape it might take as we move out of the pandemic and into whatever’s next?
Magnus Gäfvert: I think the earlier point that smaller companies can build strong solutions based on open standards and more integration is worth repeating. There are enormous opportunities lying in this approach — we just need to find a way to get there.
Michael Bogomolny: I’m not an expert in pharmaceuticals, but as I understand it, a typical vaccine development takes between three to five years — and during this pandemic we’ve just gone through, vaccines were developed within a year. We see the tremendous leap that field was able to take, and I’ve heard people in the pharmaceutical industry saying that the last year was like a decade’s worth of research and results crammed into one.
Maybe manufacturing is ready to take a similar transformative leap. I don’t see any reason why traditional manufacturing can’t explore new design and manufacturing tools, and take steps towards Industry 4.0. Maybe this is just the beginning, and we will see tremendous progress starting to take place.
Tyler Barnes: In my previous position at Autodesk, I worked on a systems modeling tool, generative design applications, and tech pubs applications, amongst other things — so, it’s fun to see innovation happening around those areas. I think all three of those spaces are ripe for innovation, and a lot of what we’re seeing at Tech Soft 3D — in terms of the new partners we’re onboarding — tracks with what we’re seeing in the broader market.
Patricia Hume: A point we brushed up against earlier is that the large OEMs are slow to move. They are dinosaurs. And the only thing I’ll leave us with is that the dinosaurs died. It took a while, but the evolution of the planet caused them to die. Technology is moving faster than the evolution of our planet, and the dinosaurs will die if they don’t adapt.
The adaptability comes through innovation, and that’s what we’re all here to do. I believe wholeheartedly that as innovators, we can trigger innovative changes in the OEMs and serve as a catalyst to move the industry in the right direction. But if the OEMs don’t evolve, customers will come to us. The more we can work together seamlessly, the more of an impact we can have in pushing innovation forward and benefitting customers.
Listen to the full conversation on SoundCloud or YouTube.