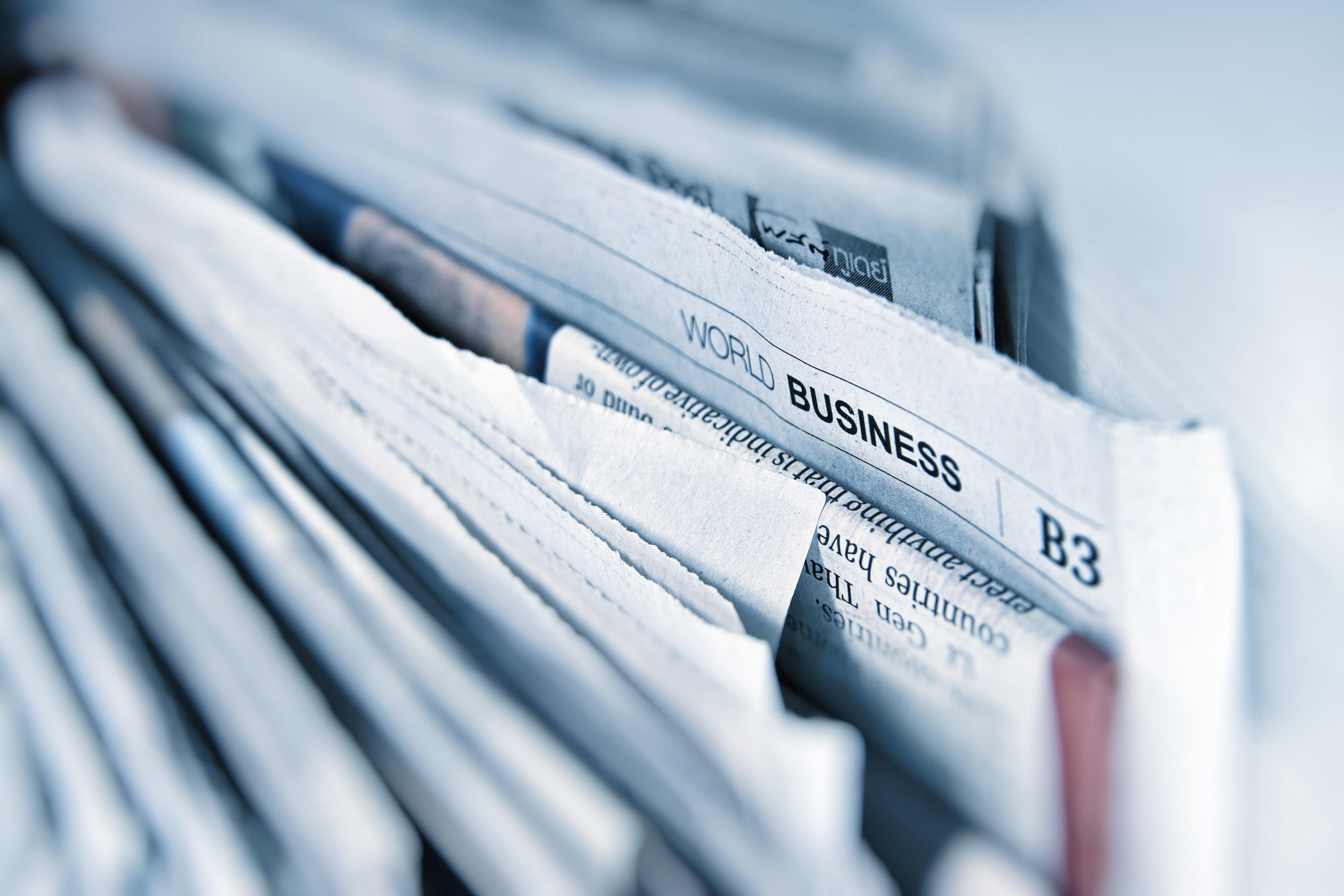
Unlocking Manufacturing Excellence with 3D Digital Twins
Manufacturers are constantly seeking innovation to enhance design efficiency, optimize vital operations, and otherwise help them get an edge in their industry. A cornerstone of these aims in modern industry is smarter, more complete data and data usage.
Enriched 3D data can allow teams to engage with designs in new ways, empowering better creativity and communication, driving innovation, and better communicating design intent. At its peak, 3D data can turn designs into interactive, immersive experiences.
3D digital twins offer dynamic virtual representations of physical structures and systems. They incorporate spatial data and real-time feedback to create interactive, highly detailed models capable of reshaping manufacturing across industries. In this piece, we will cover 5 ways digital twins can unlock manufacturing excellence. These are:
Comprehensive Visualization and Analysis
Enhanced Simulation and Predictive Analysis
Real-time Monitoring and Remote Operations
Improved Collaboration and Knowledge Sharing
Optimized Maintenance and Lifecycle Management
What are Digital Twins?
A 3D digital twin is a dynamic digital model that mirrors the physical characteristics and behaviors of a real-world entity. This virtual representation is continuously updated with real-time data ensuring accuracy and relevance. When done well, digital twins can analyze data, predict outcomes, and simulate scenarios with remarkable precision by integrating advanced analytics, machine learning, and AI algorithms.
5 Ways Digital Twins Can Empower Manufacturing
While the potential for digital twins in manufacturing spaces may vary by industry, here are five of the most common and impactful effects you need to be aware of.
Comprehensive Visualization and Analysis
One of the key benefits of 3D digital twins is their ability to provide a comprehensive visualization of complex manufacturing environments.
By integrating spatial data from sensors, CAD models, and IoT devices, manufacturers can create highly detailed virtual replicas of factories, production lines, and equipment. Visualizing data in a 3D space offers a better understanding of how components, materials, and resources interact within the manufacturing ecosystem.
Stakeholders can then explore and interact with the digital twin in a single, unified environment, gaining insights into spatial relationships, equipment layouts, and operational workflows. For example, engineers and machine operators can better analyze production processes, identify potential bottlenecks, and optimize floor layouts for improved efficiency.
This improved information allows for better decision making, problem-solving, collaboration, and overall performance enhancements for those in manufacturing spaces.
Enhanced Simulation and Predictive Analysis
3D digital twins empower manufacturers to simulate and analyze scenarios with unparalleled accuracy and realism. With this technology, organizations can model various conditions and what-if situations for their production scenarios. Real-time data streams and advanced simulation tools can integrate directly with the digital twin environment for unparalleled predictive analysis, scenario planning, and optimization of manufacturing processes.
A useful example of this is in the automotive industry. Here, manufacturers can simulate assembly line operations in a 3D digital twin, testing various production sequences, robot configurations, and material flows. These simulations and performance metrics can help identify optimal setups, reduce cycle times, and minimize production errors before implementing changes in the physical environment.
Real-time Monitoring and Remote Operations
3D digital twins can be paired with IoT sensors and other connected devices to provide real time monitoring and control of manufacturing processes. Live data streams of temperature, pressure, machine status, and production metrics, provide instant visibility into operational performance across the factory floor. This information empowers teams with better early anomaly detection, predictive maintenance, and proactive decision-making to prevent costly repairs and inefficiencies.
Remote operations become more efficient and responsive with 3D digital twins, allowing engineers and managers to monitor production activities, troubleshoot issues, and optimize workflows from anywhere.
Well-designed, immersive digital twin environments enable stakeholders to conveniently and remotely interact with their manufacturing facilities. Overall, digital twins reduce risk, enable swift problem intervention, and encourage continuous improvements in operational efficiency.
Improved Collaboration and Knowledge Sharing
3D digital twins can serve as collaborative platforms to foster cross-functional teamwork and knowledge sharing within manufacturing organizations. A unified, 3D environment for data, simulations, and analytics allows everyone from engineers and maintenance staff to production and quality assurance to seamlessly contribute to the conversation. This encourages better alignment on goals, faster and more comprehensive problem-solving, and shorter innovation cycles.
As an example, an organization’s product designers can collaborate directly with manufacturing engineers in a shared 3D digital twin environment to optimize product designs for manufacturability, assembly, and performance.
Their experience is powered by real-time collaboration tools and simulation capabilities enabling iterative design reviews, rapid prototyping, and validation cycles. The result is a better product and shorter time to market, all with more convenience for the staff involved.
Optimized Maintenance and Lifecycle Management
3D digital twins play a crucial role in optimizing maintenance strategies and asset lifecycle management within manufacturing facilities. By integrating historical performance data, sensor readings, and predictive analytics into the digital twin model, manufacturers can implement condition-based maintenance, predictive maintenance, and asset health monitoring programs.
Predictive maintenance algorithms analyze data from sensors embedded in machinery and equipment within the 3D digital twin, predicting potential failures or maintenance needs before they occur. This proactive maintenance approach minimizes unplanned downtime, extends equipment lifespan, and reduces maintenance costs. Additionally, digital twins enable virtual inspections, part replacements, and simulations of maintenance procedures, enhancing safety and operational efficiency.
Embracing the Future of Manufacturing with 3D Digital Twins
In a recent McKinsey report, the global market for digital-twin technologies is forecast to grow at about 60% annually to $73.5 billion USD over the next five years. Manufacturers who adopt this technology gain a competitive edge through enhanced operational efficiency, improved decision-making, reduced downtime, and accelerated innovation cycles. Embracing the future of manufacturing means leveraging 3D digital twins to unlock new levels of productivity, agility, and sustainability in the digital age.
Build Better Software Faster
Are you interested in building Digital Twin software? Tech Soft 3D is the leading provider of software development toolkits (SDKs) specific to 3D engineering workflows. Let us help you with powerful data import, visualization, simulation, analysis, and 3D PDF publishing. We’ve already helped power over 750 unique applications, many supporting digital twins like Unreal Engine, Rapid DCS, Visual Components, and RIB. Contact us to get started today.