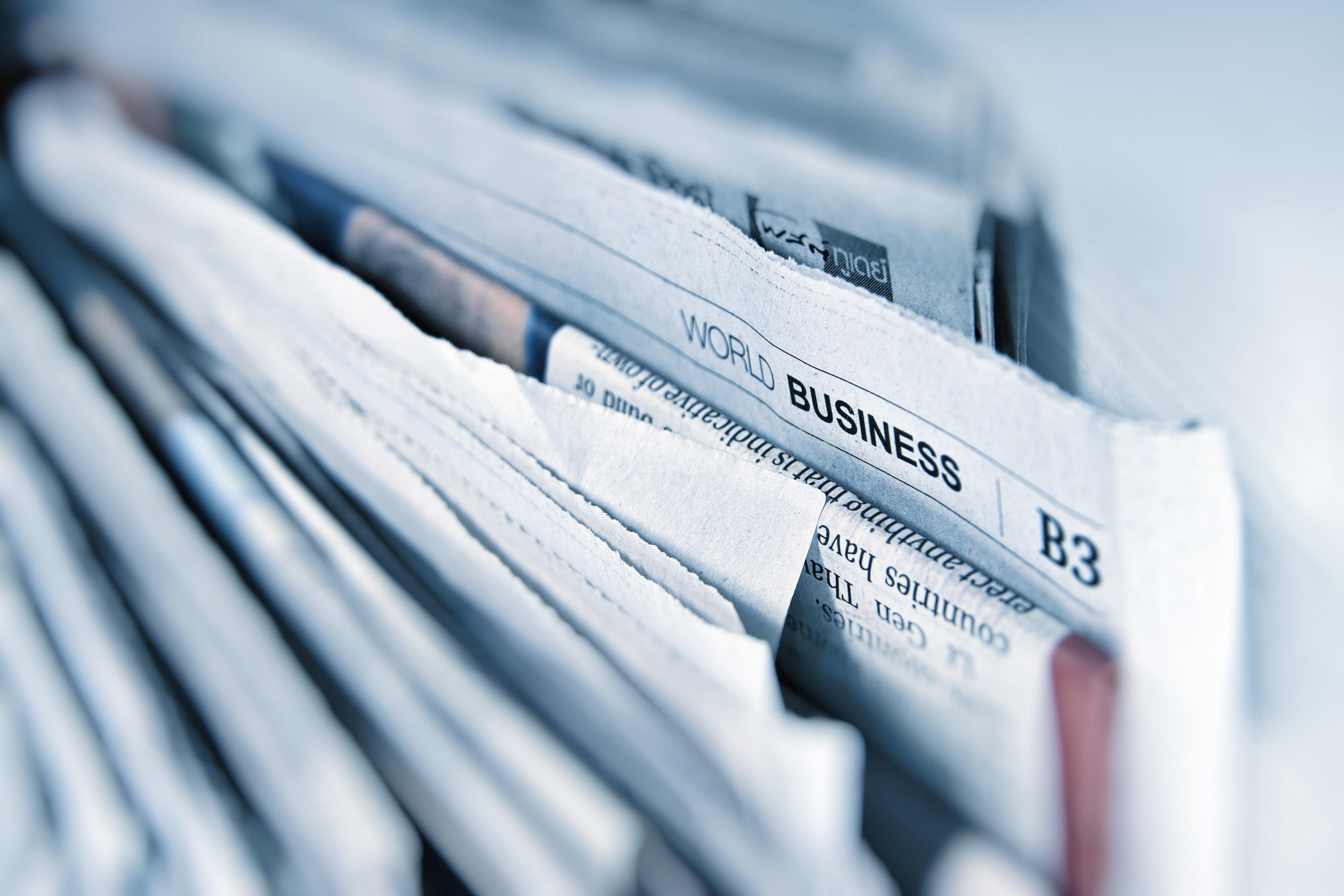
The Future of Simulation
An Introduction to Simulation
Digital simulation has been around for decades, serving various spaces such as computational physics, climatology, chemistry, biology, engineering, etc.
Taking a closer look at mechanical engineering, simulating systems before they go into production has become a very effective way for companies to test their products without incurring the expense associated with physical testing. Although a world where no such real-life testing is still far away, the question is on the table.
Beyond drastically reducing the cost of testing, simulation also allows for expanding the range of verification parts undergo before they are sent to manufacturing. Extended evaluation of a part's in-use behavior ensures a higher rate of success, or in other words, reduces the risk for companies to endure costly mistakes. For example, without modeling, it would be easy for an automobile manufacturer to overlook crucial issues that may result in car recall campaigns further down the line. This may be one of the most expensive actions a car manufacturer can take – it is essential to model a lot and to model right to lessen the margin of error.
Technology Advancements, Faster Simulations, and Increasingly Complex Problems
Let us focus on the most popular method used in engineering: the "finite element method" and its various engineering applications: structural analysis (FEA), computational fluid dynamics (CFD), material forming, electromagnetics (EM), etc.
In the early days, achieving a simulation on a mesh of 50 elements was a challenging task. Decades later, with the formidable performance increase of computational hardware and the improvements in numerical methods that have accompanied it, solving problems with millions of elements is quite common.
The model size used in a simulation determines the precision of results and gives access to analyzing more complex or smaller-scale physical phenomena.
A first observation is that once a certain precision threshold is achieved, it is useless to keep increasing model sizes – remember, this conditions the computational time. Most users will prefer to get a quick answer at the expense of marginally lower precision. They can then take advantage of the shear gain in computational speed for more beneficial tasks: run more simulations to explore the design space or run optimization algorithms.
Multi-this, Multi-that: Using Computing Power for Ever More Physics
However, for other applications, engineers gladly welcome larger models to achieve an accuracy leap by better modeling the systems they analyze.
Two current examples that come to mind in this category are multiphysics and multiscale.
The first generations of FEM simulation software were – and still are – generally modeling "single" physics: either a body being deformed OR a fluid flow OR a body being heated or cooled. Quite obviously, reality is quite different in many situations of interest.
Consider, for example, a car speeding on a wet road. On one hand, the tires are deformed by the car's weight, and on the other hand, water is flowing through the tire's ridges. Real-life tells us that water flow will be strong enough to lift the tires under some circumstances. Losing contact with the road – aquaplaning - is to be avoided at all costs, and engineers design tire ridges to minimize the risk. In a single-physics model, one would first compute the fluid flow considering the tire does not change shape, then apply the force generated by the flow on the tire, compute its deformation, and recompute the new fluid flow using the new shape of the tire, etc. Such a loose coupling of the two physics at hand – structural analysis (FEA) and computational fluid dynamics (CFD)– is a workaround to the system's true nature. A multiphysics approach will simultaneously compute the FEA and the CFD problems and provide a more accurate prediction of how the tire's ridges fight against aquaplaning.
The other "multi" field in computational mechanics that more powerful computers have opened is multiscale simulations which focus on gaining substantially better accuracy by modeling very small scale physics and applying those results to everyday FEM.
Typical FEA and CFD models operate on a macroscopic level, very far from the atoms and molecules that constitute the materials involved. In a way, they average what happens at smaller scales on the elements of the model. Today, microphysics models work directly on these smaller scales, for example, to better predict how materials behave as they are deformed or undergo thermal variations. This micro-modeling can then be put to work on your everyday macroscopic FEM to enhance the macroscale averaging and, therefore, its accuracy.
For example, engineers may want to look at how parts are manufactured through injection molding. After the molten polymer is injected into a mold, it undergoes severe changes from its initial liquid state to its final solid state. With different levels of smaller scale modeling, the behavior of the polymer as it flows, cools, and deforms is better understood.
The Cloud as Access to Computational Power
Making the formidable computational power available today accessible and easy to use for engineers is a crucial enabler of these technologies and those to come, such as artificial intelligence/machine learning for optimization problems.
These larger problems require much more than a traditional laptop or workstation. High-performance computing (HPC) –a remote workflow – is the way forward. As its usage ramps up, I'm reminded of the early days of simulation, when the user interface was a text editor and data was simply typed in. While the numerical methods and solvers needing HPC are "ready to go," the user interfaces still struggle with user-friendliness. Anyone who has been forced to work with a remote desktop understands the issue: start up a session in an unprotected environment, suffer from lag and degraded visual quality (and for IT managers: pay the price of a GPU-enabled server).
All these issues stem from the fact that using desktop user interfaces is an architectural sin within a remote workflow. With our everyday personal usage of cloud-based services, we should know better. Do we open a remote desktop for banking, hotel reservations, and booking flights? Of course not. When working on remote data, true web applications running in a browser are the only right choice.
Tech Soft 3D has unique components for remote CAE workflows to build applications that drastically improve the end-user experience while providing optimal security and cutting server costs. Beyond building these outstanding browser-based interfaces, our partners can also focus on their core added value while relying on our technology across the board: CAD import, tessellation healing, meshing, solving, interoperability and automation.
Everyone can use these tools, and everyone can – and should - benefit from them.