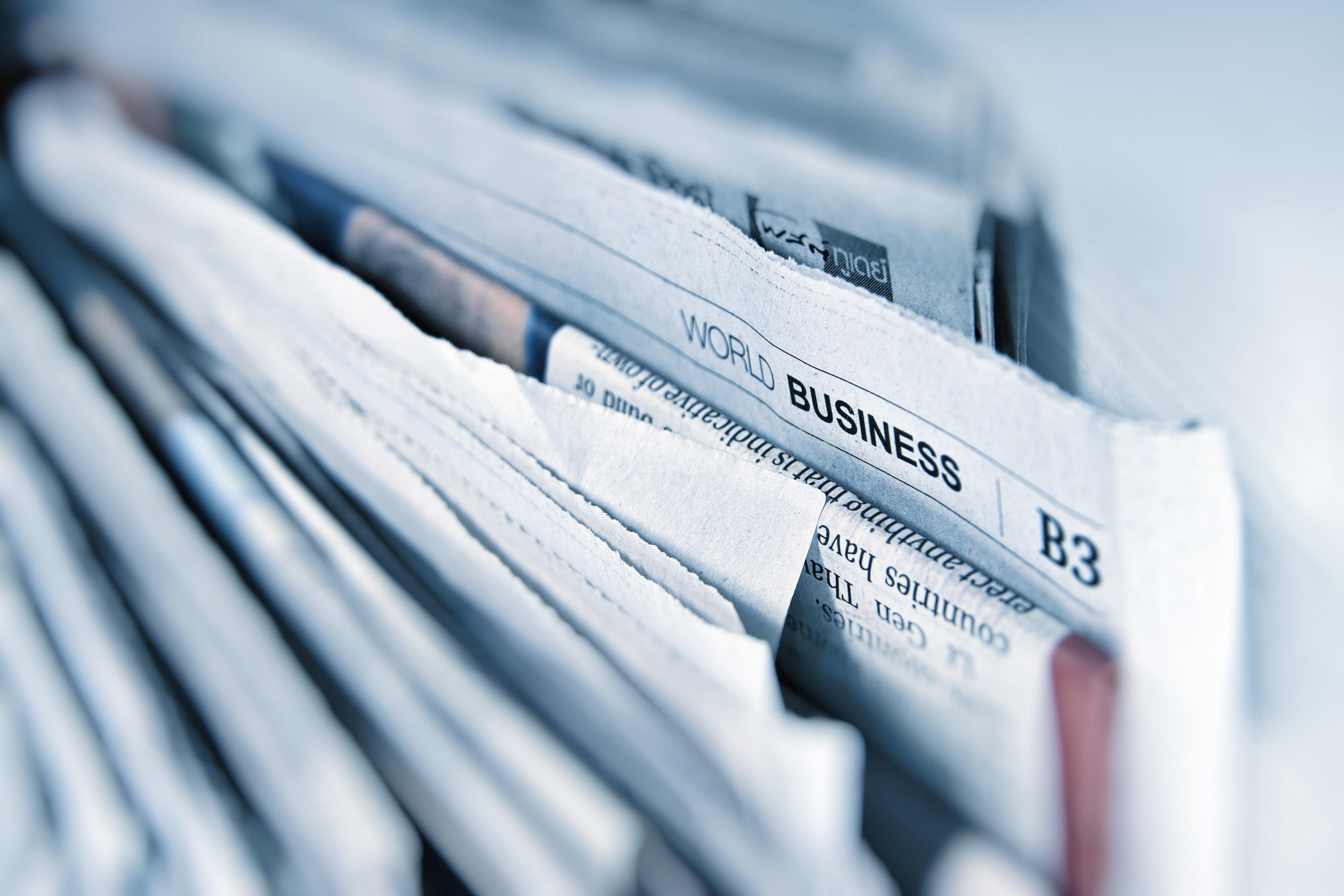
STL is Dead — It’s Time for Additive Manufacturing to Move On
In recent years, additive manufacturing has been evolving on several fronts simultaneously, helping to propel this promising technology ever further into the mainstream.
The first front is hardware — the 3D printers themselves. In the last decade, we have seen real advances in terms of the actual machinery and the efficiency and accuracy it can deliver when creating parts and components.
The second front is around materials. Gone are the days of “you can print with any material you like, as long as it’s plastic”, and the addition of new materials greatly expands the possibilities for the type of parts that can be created using 3D printing.
The third front is software, and there have been significant advances here as well. Software vendors are continually coming up with more capable and powerful additive manufacturing applications, but there is room for improvement — specifically around what file types are supported.
That’s because the STL file format, reliable workhorse though it’s been, has some pretty serious limitations, and it needs to take a back seat if 3D printing is to continue its forward march.
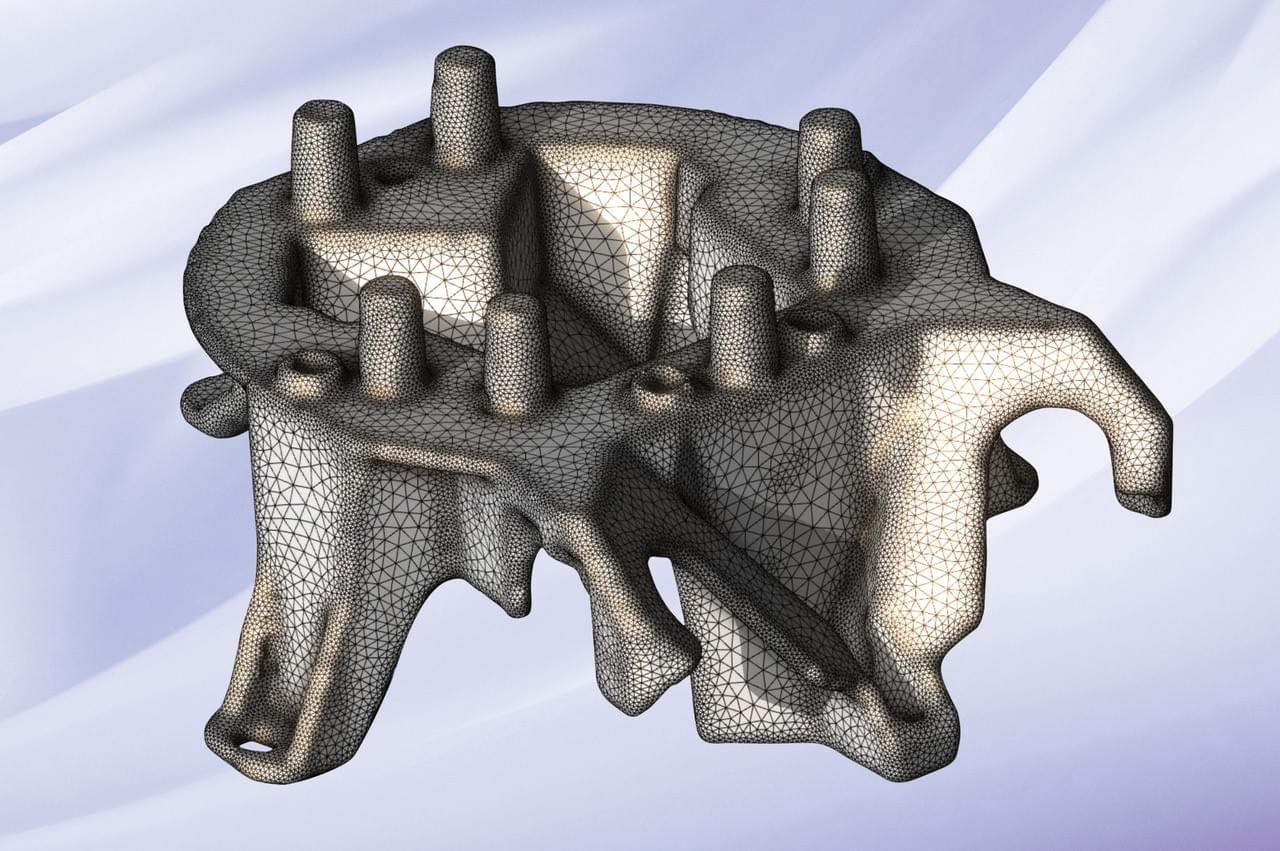
Not Exactly Ideal
Every additive manufacturing workflow boils down to the same general set of steps: You start with the CAD file of the thing you want to manufacture; you import it into an application, and maybe do a little editing or analysis to prepare it for printing; and then you push it out to a 3D printer in a format that the machine can interpret.
Historically, the STL file has been heavily used in this workflow — despite its significant shortcomings.
First of all, STL is a polygonal file format, so it’s just a group of triangles. That means that it can’t describe rounded surfaces with 100% accuracy. When creating a STL file from a CAD file, all the holes and cylinders and cones from the CAD file get tessellated, and a level of accuracy is lost during that tessellation step.
That loss of accuracy may be a problem when you go to manufacture the part. For example, if you have two components that you’re producing that need to mate to one another within a certain tolerance, the tessellated version might not be precise enough.
Additionally, the STL file format was designed decades ago, so it doesn’t really lend itself to a more modern assembly structure approach. It doesn’t capture color, texture, or material structure, and it can’t embody additional information around design intent, such as product manufacturing information or dimensions and tolerances. All of that data is captured in the original CAD file, of course, but it’s lost when saving to STL.
So, if STL is less than ideal — and if newer file formats like 3MF are an improvement, but still lacking in the level of detail they can provide — what’s a better way forward?
Straight to the Source
Ideally, 3D printing applications should be able to tap into the original CAD file. The CAD file simply provides richer data than either an STL or a 3MF.
Having access to the assembly structure, BREP (boundary representation), product manufacturing information, and dimensioning and tolerances — along with the other data inside those CAD files — allows users to make intelligent decisions about how they’re going to print an object.
Imagine a quoting system, where people are uploading files to an online system and the manufacturer creates an automated quote for the customer. That detailed level of data around things like product manufacturing information is going to be important because the manufacturer needs to know which of their machines is going to be able to hit those tolerances, and that’s going to affect the cost that they quote.
Simply put, STL can’t deliver the same results. The ability to go to the original CAD file opens the door to the development of a more powerful class of additive manufacturing applications, and helps point the way forward for the industry.
One Foot in Both Worlds
Does the above mean “rest in peace STL, long live CAD?”
Well, not exactly. The simple fact is that there’s still a ton of STL data out there; many of the libraries that customers are still working with, and many of the files they’re receiving, are STL files.
Additionally, there is a tremendous amount of mesh data coming from the manufacturing world. This data could be from reverse engineering efforts, which typically involves point scanning a part, or it could be from terrestrial scanning of massive architectural models — and customers need to be able to work with all of this mesh data.
To cover their bases and serve the widest range of customers possible, then, additive manufacturing developers will want to keep a foot in both worlds and provide a solid modeling environment that can work with the CAD file natively, in addition to mesh tools.
For example, a customer might need to quickly eliminate any overlapping triangles or perform other quick fixes on the mesh. Maybe the surfaces are too thin and need to be thickened. Alternately, they may want to hollow out the solid to save on material cost, or offset up to account for shrinkage during cooling. Mesh tools ensure that that’s no problem.
Likewise, the customer who wants to directly work with the CAD file and make a few tweaks to prepare it for printing can do so if there are solid modeling tools built into the application that can perform edits on the CAD data.
Of course, these two worlds aren’t entirely separate from one another: Sometimes, mesh data and solid data are brought together in the same assembly. This creates a need for tools that do both solid modeling and polygonal modeling, and then bring them together into something called a convergent modeling or hybrid modeling environment. This fusion of the two approaches is an exciting area where quite a bit of innovation is occurring right now.
As long as software developers have the right building blocks — around importing data in a variety of file formats, visualizing it, and then enabling end users to easily work with solid or polygonal data to prepare it for printing — they will be able to create powerful additive manufacturing applications that meet the needs of the market.
The key is to not be artificially restrained by the limitations of STL — but to keep an eye on where 3D printing can go in the future, what’s possible, and how it can continue to evolve in exciting new directions.