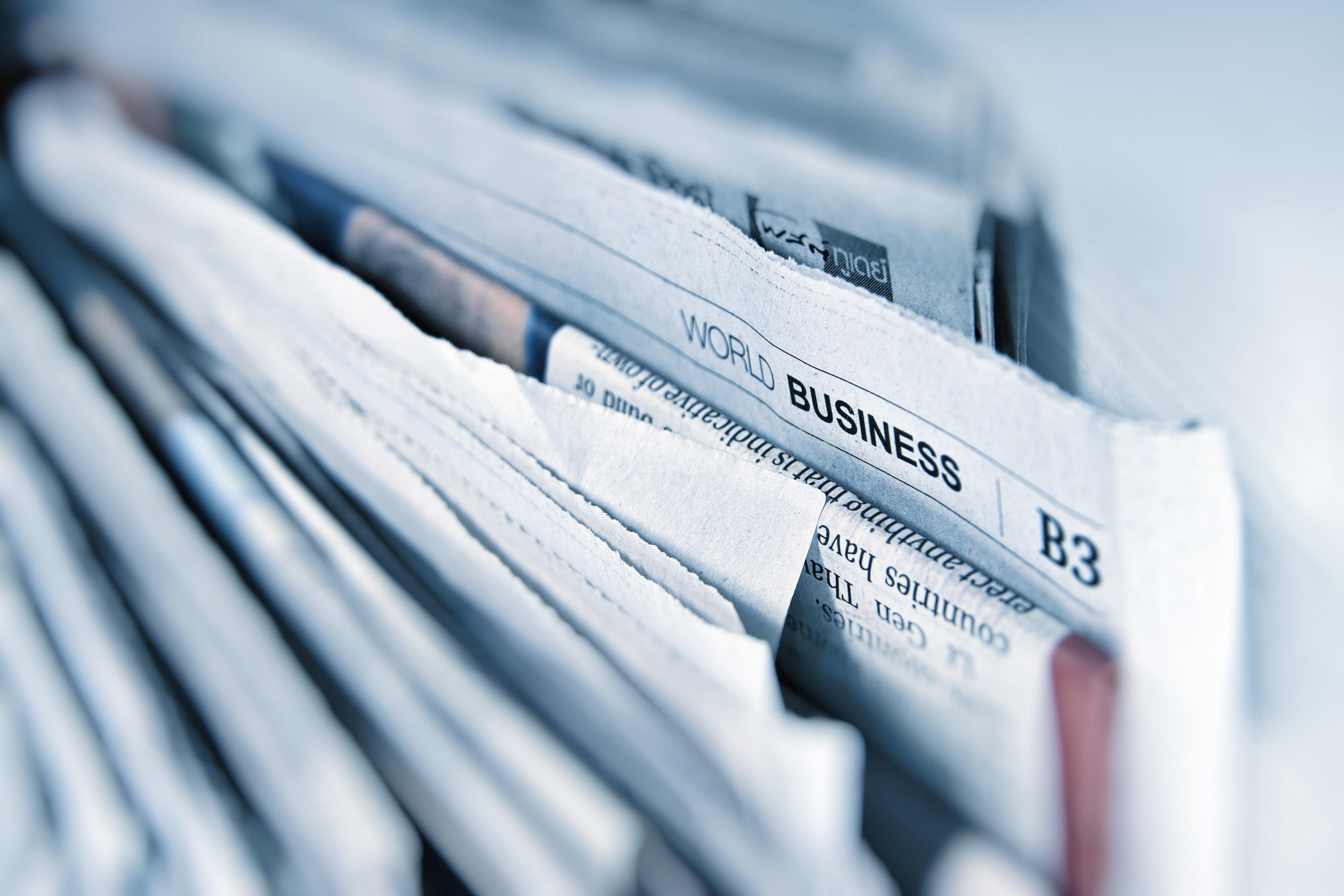
Remote CAE Visual Workflows: Sharing and Collaborating More for Less
As we take our breath seeing a second wave cover the planet, the opportunities to enÂgage in meaningful changes are popping up everywhere. In a previous blog, I discussed the benefits of telecommuting and introduced the idea that technology is the key eleÂment to its success.
In the CAE space, this translates into offering engineers a high-quality, secure, comforÂtable, and cost-effective set of tools to remotely conduct their calculations, then analyze and share their results with others. Most of these requirements on a remote office focus on the user interface and the access it gives to visualizations of the models under study.
The same blog concluded that to achieve this, WebGL-based client-side rendering was in most cases a no-brainer: win-win for employers and remote employees and problem solved. There are also a few rare situations where remote desktop connections remain necessary – e.g. XXL models – but is “the exception that confirms the rule” as we say here in France.
But visualization is only a part of the engineering workflow. In this article, I will dig into a broader view of the CAE engineer’s practices and needs, and introduce a new “all-you-can-eat” toolbox we have put up here at Ceetron: Visual Workflows.
“Cross-solver, automated and remotely accessible” is how I would describe the modern CAE engineer’s environment, especially when focusing on large organizations. Each of these characteristics has its share of pain and gain worth discussing.
One environment fits all: the quest of the Holy Grail
In the late 2000s and early 2010s, major CAD providers such as Autodesk or Dassault Systèmes engaged in an acquisition frenzy of simulation ISVs, in an attempt to establish unified platforms for both modelling and simulating.
Not all ISVs ended up as modules in CAD systems however, and they themselves have continued to grow more often externally than not, especially over the last 10 years. Ansys, MSC, ESI (and others) all have a broad offering of simulation tools, eventually trying to fully respond to end-user’s needs as their CAD counterparts did before them.
These strategies have never fully worked. My hunch is that the high technicity and speÂcificity of the solvers means that it’s hard to create the offering that fits all. It’s a sound objective, but the reality is that large end-user organizations will pick and choose their solvers. And sometimes it’s not even a technical choice, it may be because of legacy or the personal preference and experience of the CAE manager.
A CAE engineer’s environment is cross-solver – with all the pain that implies: different file formats, different elements, different results (mappings that change from elements to nodes, and what to do then ?) … and the necessity to master multiple software environÂments to access these tools.
Automation: the common practice of engineers
Every engineer has an optimizer implanted in his or her brain. It’s a fact of life. Whenever something can be done faster or better – within reasonable cost – the engineer will strive at implementing the better of faster way.
The reasons for automating what can be in the simulation lifecycle are multiple: the cross-solver environment we just discussed, a more efficient use of engineer-hours, inÂcreasing the number of simulations for extended analysis, etc.
Reference: Robinson, M.A. (2010), An empirical analysis of engineers’ information behaviors. J. Am. Soc. Inf. Sci., 61: 640-658. doi:10.1002/asi.21290
The benefits of reducing manual intervention in the simulation process are such that an entire branch of the CAE community – SPDM (Simulation Process Data Management) has focused on developing platforms to implement automation and improve data manageÂment and sharing. Esteco, PDTec, Aras, Noesis Solutions, Arc Advisory Group and many others propose a wide range of tools to streamline engineering workflows across solvers, promote collaboration and optimize the simulation process. Of course, the big names in simulation have their own SPDM solutions as well: MSC SimManager, Ansys Engineering Knowledge Manager, Siemens CAE Simulation Management, etc.
However, according to CIMdata’s PLM report (2018): “Industry estimates indicate that well under five percent of all simulation and analysis specialists worldwide use some form of commercial simulation data management technology to manage and archive their S&A models and to collaborate with other simulation specialists as well as other design disciplines within their organizations,”
Note that this ridiculous percentage does not include in-house automation procedures. At Ceetron, we provide remote interactive CAE visualization software components and Python automation modules to both commercial SPDM providers and in-house end-users. Of course, we have not conducted a large-scale survey, but our hunch is that a lot of companies are developing and/or maintaining in-house automated workflows tools, which would mitigate the true usage of the technologies. The processes involved are quite strategic, so keeping tight control may make sense to some users.
Remote CAE Visualization: key to streamlined workflows sucÂcess
One of the core components of SPDM is exposing data to all stakeholders. Whether the streamlined workflow is implemented in-house or bought from an external vendor, siÂmulations results will be stored and archived in well determined locations.
This serves two purposes: a) facilitate the access and search within these large amounts of information, i.e. act as a knowledge base repository and b) enable global algorithms to work on populations of simulations – optimization is a popular use case but machine learning is catching up.
The way users access this data remotely is a key element in the success and efficiency of the SPDM systems. It’s nice to type a keyword and instantly gain access to all related simulations. It’s even nicer if results are available in the natural 3D interactive way expecÂted by CAE engineers.
Ceetron’s cloud-native WebGL visualization technology focuses on this engineer-quality remote visualization, providing remote access that is secure and comfortable, with high visual quality and at a reduced cost.
The client-side rendering gives browser-based applications the usage comfort and visual quality of their classical desktop counterparts.
Minimizing the amount of data that leaves the server is the best way to avoid security leaks: only what is displayed leaves the organization’s IT system / private cloud / public cloud.
Finally, since the rendering is done on the client device, no GPU is required on the server which lowers its cost 5 to 10-fold.
Ceetron Visual Workflows: an “all you can eat” CAE engineeÂring workflow toolbox
Five years after its first release, Ceetron’s cloud-based visualization technology is mature and well established in the CAE market both among ISVs and end-users. What we have observed for the latter is that it was not uncommon for them to buy multiple Ceetron products and assemble them to achieve efficient workflows either from scratch or inteÂgrating some larger pre-existing systems.
This is why we have decided to leverage the visualization technology and now offer “CeeÂtron Visual Workflows” : a range of cross-solver tools to develop and automate post-proÂcessing workflows around the idea that remote CAE results should be accessed from anywhere and on any device, in 3D of course, and interactively – not by sending e-mails or sharing folders with plots, 2D images or videos.
Ceetron Visual Workflows are made up of 3 sets of tools, each addressing key stages of your workflow.
Analysis
This first set of tools focuses on generating the “analysis models” that will be stored and shared remotely with all your peers. Analysis models are 3D interactive snapshots of whatever post-processing you are doing, e.g. an animation of displacements with two cutting planes or a particle trace animation + an iso-volume
Words are nice, but the true stuff is self-explanatory. Here below is an analysis model:
https://cloud.ceetron.com/v/cee_vorsch_cloud?startAnimation=1
This first set of tools allows interactive analysis model generation either locally or remoÂtely, using our post-processor Analyzer. It also includes a Python API to automate the process. If you have C++ development resources, you can even build a custom applicaÂtion to handle the analysis model generation. It’s up to you.
As all of Visual Workflows, all these software work on a wide range of industry standard results: Abaqus, Ansys, Nastran, OpenFOAM, Fluent, LS-DYNA, Ensight, Hyperworks, etc.
Sharing Portals
The next set of tools addresses the storage of the analysis models generated previously.
The simplest portal is ours: cloud.ceetron.com. You get subscriptions and storage space on this portal. Most of the time, this is used for testing or evaluation purposes. If you are concerned with security, your best bet is to install the same type of portal within your own IT system or wherever you feel comfortable – we have a product for this. If all else fails and you want something more custom or with richer features, you also have access to the underlying SDK to build your own portal.
Remote Viewers
The analysis models on your portal are now accessible from anywhere on any device that has a browser: workstation, laptop, mobile phone, tablet, … even on a Smart TV. Our CTO enjoys his 3D models on the screen of his Model 3 Tesla.
We provide ready-to-use viewers, as well as a range of desktop-based sharing applicaÂtions which sometimes come in handy (insert analysis models in Powerpoint for exaÂmple). There is even a VR viewer for Oculus Rift owners.
And as always, you can build your own viewer whenever you are ready using the underÂlying SDK.
With Ceetron Visual Workflows, we have done our best to show the value of our techÂnology once the bits and pieces are put together. The toolbox is yours: build new workÂflows, enhance old ones, or just enjoy sharing CAE data the way it should be.